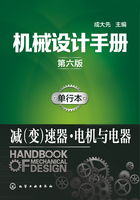
2.2 风力发电用增速齿轮箱设计
2.2.1 概述
风电齿轮箱(图17-1-26)的研究随着绿色能源发展及应用逐渐发展成熟,早期盛兴于欧美,近20年来在国内取得长足发展。功率级别涵盖750kW~8MW,国外10MW样机也在研制之中。

图17-1-26 风电齿轮箱外形图
本节主要介绍风电齿轮箱的特点、技术趋势,以一款750kW齿轮箱为例,介绍其设计过程、校核计算方法、优化过程及测试情况。
2.2.2 特点及技术趋势
风电齿轮箱是风力发电传动链中的核心零部件之一,用于主轴和发电机之间的功率传递。由于机舱通常安装在风力资源丰富的高原、海上及其他较偏远地区,安装、运输条件差,零部件维护及保养困难,因此对其可靠性提出了很高的要求。区别于其他机械传动系统,风电齿轮传动系统有其自身特点如下。
①随着单机容量逐渐增加,单纯依靠增加齿轮设计尺寸的做法既不经济又难以满足设计要求,硬齿面技术的发展有效改善了这一现状,显著提高了齿面承载能力,并且提高了传动精度,使材料的性能得到充分发挥。硬齿面技术推广以后,热处理以及齿面修形等工艺的得到极大发展。
②低转重载,大扭矩使轮齿产生较大变形,在啮入啮出位置容易产生冲击载荷,导致局部接触应力过高;另一方面,大扭矩使齿面润滑条件恶化生产不稳定油膜,引起磨损并导致局部温升严重,进而影响齿轮使用寿命。
③工况复杂,由于风机在高空安装,地点偏远且经常具有沙尘、盐雾气候,同时需要承受较大温差,因此使用工况比较恶劣。
④风速变化导致载荷非恒定,高空风速不稳定使得轮齿载荷波动更为显著,这种时变载荷对于齿轮啮合动力学特性以及可靠性均有较大影响。
⑤为了保证齿轮箱安全运行,齿轮箱润滑冷却系统中增加了离线过滤、颗粒传感器等精密装置,极大程度提高了润滑油的清洁度。
⑥为了进一步减小外形尺寸,无外圈轴承技术逐渐在行星轮上推广,将行星轮内孔作为轴承外滚道,进一步减小了传动体积。
同时,随着承载功率不断增大,风电齿轮传动技术呈现出以下3个特点。
①硬齿面技术,随着承载能力逐渐提高,增加齿轮尺寸在经济性及实用性上受到很大挑战,硬齿面技术发展改善了这一现状,显著提高齿面承载能力及传动精度,使材料性能得到充分发挥也推动了热处理及齿面修形工艺的发展。
②功率分流,功率分流技术可有效减少单个轮齿载荷,但同时也使得轮齿在参数设计,安装以及加工过程中产生一些限制条件,尤其是由此造成的偏载和振动问题尚有许多工作需要开展。
③模块化设计技术是单个设计到批量化、规模化设计的必经之路,是提高设计效率及提高性能指标的重要保证措施,成熟的模块化设计可以提高生产力并衍生新的同类产品,模块化设计程度是衡量一个企业设计能力乃至规模的重要指数。
2.2.3 750kW风电齿轮箱设计举例
(1)总体技术条件
主齿轮箱总体要求见表17-1-41及表17-1-42。
表17-1-41 气候条件

表17-1-42 总体技术要求

(2)传动方案设计
风电用增速齿轮箱常用传动结构有一级行星加两级平行轴(见图17-1-27)、两级行星加一级平行轴(见图17-1-28)、双行星联动一级平行轴结构(见图17-1-29)、功率分流型结构(见图17-1-30)等。对于2MW及其以下功率的增速齿轮箱,图17-1-27以及图17-1-28所示的两种结构已逐渐趋于成熟并形成批量化生产能力。本设计采用如图17-1-28所示的传动结构,前两级为NGW行星传动,最后一级采用平行轴传动。

图17-1-27 一级行星两级平行轴结构
1—内齿圈;2—太阳轮;3—行星轮;4—行星架;5—第二级大齿轮;6—第二级小齿轮;7—第三级大齿轮;8—第三级小齿轮

图17-1-28 两级行星一级平行轴结构
1—第一级内齿圈;2—第一级太阳轮;3—第一级行星轮;4—第一级行星架;5—第二级内齿圈;6—第二级太阳轮;7—第二级行星轮;8—第二级行星架;9—第三级大齿轮;10—第三级小齿轮

图17-1-29 双行星联动一级平行轴结构
1—第一级内齿圈;2—第一级大行星轮;3—第一级行星架;4—第一级小行星轮;5—太阳轮;6—第二级小齿轮;7—第二级小齿轮

图17-1-30 功率分流型结构
1—第一级内齿圈;2—第一级太阳轮;3—第一级行星轮;4—第一级行星架;5—第二级太阳轮;6—第二级行星轮;7—第二级行星架;8—第三级大齿轮;9—第三级小齿轮
(3)材料及热处理方式选择
采用硬齿面,材料牌号及热处理方式见表17-1-43。
表17-1-43 齿轮材料性能及热处理要求

(4)参数粗配
行星传动级的行星轮个数取np=3,考虑行星轮系的装配条件以及同心条件,同时按照等滑差率原则分配变位系数。基本配齿参数如表17-1-44所示。
表17-1-44 基本配齿参数

(5)几何参数计算
按照角度位齿轮传动几何计算,各级传动的主要几何参数(含主要刀具参数)计算结果如表17-1-45~表17-1-47所示。
表17-1-45 第一级行星传动几何参数

表17-1-46 第二级行星传动几何参数

表17-1-47 第三级平行轴传动几何参数

(6)齿轮强度计算
1)载荷谱及当量载荷
在图17-1-31坐标系下,风场对齿轮箱的LDD载荷谱如表17-1-48所示,根据ISO 6336-6中加权平均进行载荷处理。

图17-1-31 风机转动坐标系
XR—沿风轮旋转轴方向;ZR—径向,指向风轮叶片1方向且与XR垂直;YR—与XR垂直(XR、YR和ZR组成右手系)
表17-1-48 LDD疲劳载荷谱

式中,ni为第i个载荷步的转速;Ti为第i个载荷步的扭矩;p为woehler损伤曲线的斜率。
根据上式可得作用于该齿轮箱的输入当量扭矩Tequ如下:
Tequ=252.702kN·m
同时按照下式可求得各级小齿轮切向载荷Fti:
式中,Ti为某级小齿轮扭矩,kN·m;di为某级小齿轮分度圆直径,m。
2)接触强度计算系数及选取
齿轮接触疲劳强度及弯曲疲劳强度中算过程中涉及大量修正系数,合理选择系数是确保安全系数计算正确的前提,下面以第一级行星传动的太阳轮为例进行介绍。
①使用系数KA。根据GB/T 19073—2008对于使用系数的规定,当具有真实载荷时,使用系数KA取值为1。
②动载系数KV。
齿距偏差的极限偏差:
传动精度系数C:
取C=6,同时有
B=0.25(C-5.0)0.667=0.25
A=50+56×(1.0-B)=92
于是有
③齿向载荷分布系数KHβ。按照一般方法计算KHβ,由于采用硬齿面传动,取跑和系数xβ=0.85,啮合刚度系数cγ=20N/(mm·μm),同时,螺旋线总偏差Fβ为
加工、安装误差产生的啮合齿向误差分量fma为
fma=0.5Fβ=8.75(μm)
则啮合齿向载荷分布系数KHβ为
④齿间载荷分布系数KHα。第一级太阳轮切向载荷为
由于是5级硬齿面,因此取KHα=KFα=1.1。
⑤单对齿啮合系数ZB、ZD。由于轴向重合度εβ>1,取ZB=ZD=1。
⑥节点区域系数ZH。基圆螺旋角:βb=7.515°,端面压力角αt=21.472°,端面啮合角:。于是有
⑦弹性系数ZE。根据齿轮材料,取弹性系数ZE=189.8MPa。
⑧重合度系数Zε。
⑨螺旋角系数Zρ。
⑩寿命系数ZNT。按照20年设计寿命计算,第一级太阳轮的应力循环次数约为0.86×109次,按照下式计算寿命系数:
润滑剂、速度、粗糙度系数(ZLZVZR)。按照持久长度以及加工方法,由于采用滚齿加磨齿加工,取ZLZVZR=0.92。
工作硬化系数Zw。由于热处理后齿面硬度达到(60+2)HRC,因此取ZW=1。
尺寸系数ZX。
ZX=1.076-0.0109mn=0.9452
接触强度极限σHmin。18CrNiMo7-6经过渗碳淬火热处理后,其硬度可以达到(60±2)HRC,接触强度可达σHmin=1500MPa。
3)接触强度校核
接触强度计算安全系数SH:
符合GB/T 19073中关于齿面接触安全系数大于1.25的要求。
4)弯曲强度计算系数及选取
①齿向载荷分布系数KFβ。
②齿形系数YFa。采用标准刀具进行加工,αn=20°,hap/mn=1.0,hfp/mn=1.25,ρfp/mn=0.38。当量齿数为zv=z/(cos2βbcosβ)=24.66,变位系数为0.251,由图解法得YFa=2.48。
③应力修正系数YSa。同上,当量齿数为zv=24.66,变位系数为0.251,应力修正系数也可由图解法得YSa=1.65。
④重合度系数Yε。
当量齿轮的端面重合度为
重合度系数按下式计算:
⑤螺旋角系数Yβ。螺旋角系数按照下式计算:
⑥试验齿轮应力修正系数YST。一般情况下取YST=2.0。
⑦寿命系数YNT。按照20年设计寿命计算,第一级太阳轮的应力循环次数约为0.86×109次,按照下式计算寿命系数:
⑧齿根圆角敏感系数YδrelT。齿根圆角敏感系数YδrelT近似取1。
⑨齿根表面状况系数YRrelT。根据齿轮材料及表面粗糙度,近似由图解法取YRrelT=1.0。
⑩尺寸系数YX。由于齿轮材料为渗碳淬火钢材,法向模数为12mm,由图解法查得YX=0.97。
弯曲强度极限σFmin。18CrNiMo7-6经过渗碳淬火热处理后,其硬度可以达到(60±2)HRC,接触强度可达σFmin=500MPa。
5)弯曲强度校核
弯曲强度计算安全系数SF:
符合GB/T 19073中关于齿面接触安全系数大于1.55的要求。
6)其他齿轮啮合强度计算
计算过程类似,省略计算过程,将其他各级齿轮啮合安全系数计算结果汇总如表17-1-49所示。
表17-1-49 各级安全系数

很显然,相对于GB/T 19073中关于风电齿轮箱齿轮安全系数的规定,粗配方案的安全余量过大。有必要进行配齿优化。
(7)配齿参数优化
为使传动结构更经济、紧凑,确保传动可靠性,调整各级传动参数,调整后配齿参数如表17-1-50所示:
表17-1-50 优化后的基本配齿参数

按照这些参数重新计算各级传动的齿面接触安全系数以及齿根弯曲安全系数,同样将计算过程省略,将计算结果列入表17-1-51中。
表17-1-51 优化后的各级安全系数

从表17-1-51中可以看出,首先,各级安全余量均满足GB/T 19073中规定的强度要求,并且表现出良好的一致性趋势;另外,相对于粗选参数,优化后的安全系数分布更合理,高速级为了便于后续速比配选新设计,保留相对偏大的安全余量是有必要的。
(8)结构设计
1)支撑方式设计
风电齿轮箱在机舱的安装支撑方式大体上分为一点、两点以及三点支撑方式。
其中,一点式支撑齿轮箱与轮毂直接连接,形成悬臂之势。这种支撑形式优点在于其结构十分紧凑,有利于机舱部件布置及散热,缺点是叶片颤振会传递到齿轮箱,不利于齿轮啮合的稳定性。
两点支撑形式齿轮箱通过主轴与轮毂连接,主轴通过两个主轴承平衡轮毂传递的倾覆弯矩,因此齿轮箱主要承受切向扭矩,这种机构齿轮箱载荷形式简单,但主轴及主轴承增加了设计成本。
三点支撑(如图17-1-32所示)相对于两点支撑,主轴上少用了一个主轴承,减少了设计成本,但齿轮箱需要承受部分弯矩,这部分载荷最终将反映到箱体以及内部轴承上。

图17-1-32 三点式支撑方式
2)轴承选用
轴承选型是风电齿轮箱传动系统设计过程的重要过程,不同型号轴承的受力特点有着显著区别,同时支撑、定位形式对于改善轴系受力并提高轴承自身使用寿命也有着重要的影响。
对于主轴支撑轴承,考虑到其径向载荷大同时承受轴向载荷,并且叶片的颤振要求主轴轴承具有一定调心能力,因此主轴轴承选用双列球面滚子轴承(见图17-1-33),具有两列滚子,外圈共用球面滚道,内圈有两个滚道,可同时承受径向以及轴向载荷,对于高空复杂载荷适应能力也较强。

图17-1-33 主轴-第一级行星架轴承配置形式
对于行星架的支撑方式,由于行星轮的不均载性及自身质量,支撑轴承也承受径向载荷,同时由于采用斜齿轮传动,导致行星架轴承将承受轴向载荷。因此在选用行星架支撑轴承时需要综合考虑径向以及轴向载荷及其比例关系,同时考虑空间尺寸限制,第一级行星架和主轴相连,其下风向选用满装圆柱滚子轴承,径向承载能力大,同时具有一定轴承承载能力;而第二级行星架轴承则选用球轴承(上风向)和单列圆锥轴承(下风向)相配合的形式,见图17-1-34。

图17-1-34 第二级行星架轴承配置形式
对于行星轮支撑轴承选型,由于第一级功率密度大,对轴承径向承载能力要求很高,因此选用双列满装圆柱滚子轴承,两套对称布置,因子滚子数量多,承载能力大幅提高,见图17-1-35;第二级行星轮由于转速相对较高,采用满装轴承容易引起摩擦发热,因此采用NJ型单列圆柱滚子轴承,两套对称布置,中间利用隔套定位,安装方便且允许转速高,见图17-1-36。

图17-1-35 第一级行星轮轴承配置形式

图17-1-36 第二级行星轮轴承配置形式
在平行级传动中,轴承选型有以下几种形式:
①单列圆柱轴承加双列圆锥轴承配合,轴向力由圆锥轴承提供;
②两套单列圆锥轴承组合使用;
③两套单列圆柱轴承组合使用,如有轴向分力,还可以增加一个止推球轴承;
④两个角接触球轴承与圆柱滚子轴承轴承组合使用,轴向载荷由角接触球轴承承担。
关于轴承的配合、定位方式、游隙选择,安装方式等,各企业都有自己的风格并逐渐形成成熟方案,这里不作过多介绍。
3)润滑冷却系统设计
风电齿轮箱润滑冷却系统是风电齿轮箱的重要组成部分,润滑冷却系统的设计,必须满足润滑冷却系统技术
规格书的要求,该规格书通常经过风力发电机组主机厂、齿轮箱生产厂以及润滑冷却系统专业生产厂等相关单位共同商定并得到相关各方的认可。
风电齿轮箱的润滑冷却系统,主要由供油泵、过滤器、温控阀、压力阀、安全阀、冷却器、胶管组件以及油箱等部件组成。
供油泵通常采用双速电动齿轮泵(又称电动泵),在油温较低时低速运行,在油温升高后由控制系统切换至高速运行。此外,在风力发电机组制动过程或意外停电时有可能产生短暂的缺油,从而引起机件的损伤,为了较好地解决此问题,还需要设置双向齿轮泵(又称为机械泵),该齿轮泵一般安装在风电齿轮箱的输出侧,由风电齿轮箱通过一对齿轮来驱动。上述两种供油泵的出口均需要设置安全阀,开启压力一般设定在12bar左右,以防止压力过高对系统元件造成损坏。
过滤器通常采用两级过滤,一级为粗过滤,过滤器精度一般为25μm或50μm,另一级为精过滤,过滤器精度一般为5μm或10μm。当冷启动时或当过滤器滤芯压差大于某一数值(一般为4bar)时,润滑油只经过粗过滤,当油温逐渐升高或当滤芯压差小于该数值时,润滑油经过精过滤和粗过滤两级过滤。在风电齿轮箱正常工作时,过滤元件必须保证润滑油的清洁度不低于ISO 4406的18/15/12等级。
过滤器应配备压差发讯器,当滤芯堵塞压力达到某一数值(一般为3bar)时发出报警信号,提示更换滤芯。过滤器应配备止回阀(开启压力一般为0.2bar),以便于滤油器的维修。过滤器顶部应设置排气孔,工作过程中产生的气体通过管路排入风电齿轮箱。
当系统总流量较小时,电动泵和机械泵可以共用一个过滤器,当系统总流量较大时,电动泵和机械泵需要各自配备一个独立的过滤器。此外,根据结构的要求,可以将电动泵与过滤器集成在一起,组成一个紧凑式的供油装置,通过支架固定在风电齿轮箱上。
温控阀控制油流的方向。当油温较低(一般为<45℃)时,绝大部分润滑油不经过冷却器冷却而直接进入风电齿轮箱,当油温较高(一般为>60℃)时,全部润滑油均经过冷却器冷却后再进入风电齿轮箱。
冷却器可根据需要,采用风冷却器或水冷换热器。对于风冷却器,驱动冷却风扇的电机可以采用双速电机。当油温达到某一数值(譬如55℃)时,冷却器电机启动,当油温再次降至某一数值(譬如45℃)时,冷却器电机关闭。风冷却器应配备旁通阀,当冷却器前后压差达到某一数值(譬如6bar)时,旁通阀开启,润滑油不经过冷却器而直接进入风电齿轮箱。在风电齿轮箱润滑冷却系统中,通常使用胶管组件将供油泵、过滤器以及冷却器等部件连接起来。胶管组件的内表面必须耐润滑油,外表面必须耐各种稀油和干油,爆裂压力一般大于60bar。
在风电齿轮箱润滑冷却系统中,通常将齿轮箱的底部空间作为储存润滑油的油箱,但对于某些结构较为特殊的齿轮箱,需要设置独立的外部油箱。
根据ANSI/AGMA/AWEA 6006-A03,对于以箱体为油池的多级齿轮箱,润滑冷却系统的最小油量应为Qty=0.15Pt+20,其中,Qty为建议油量(经验值),单位为升(L),Pt为风力发电机组额定功率,单位为千瓦(kW)。在通常情况下,润滑冷却系统的油量可以按3~5倍的系统润滑油流量选取。
在风电齿轮箱润滑冷却系统中,需要配备监测油压的压力传感器、监测油温的温度传感器、监测油位的液位计以及预热润滑油的电加热器。
近年来,随着对风电齿轮箱润滑冷却系统认识的不断深入,根据不同的使用场合和用户的需要,一些风电齿轮箱润滑冷却系统新增了离线过滤装置,离线加热装置以及颗粒传感器等部件,这些部件对于风机齿轮箱安全可靠的运行具有重要的作用。
图17-1-37为某型风电齿轮箱润滑冷却系统原理图。

图17-1-37 某型风电齿轮箱润滑冷却系统的原理图
(9)传动性能及结构优化
1)齿轮修形
齿轮在啮合过程中,由于加工误差及弹性变形使被动齿轮的实际基节大于主动齿轮的实际基节,从而产生边缘冲击,这种边缘效应会影响齿轮传动的平稳性,产生过大噪声。
①齿顶修形 传统修形方法是基于经验公式计算,并且修形量都是基于模数、切向载荷及齿宽等基本参数的经验计算,但是这种方式通常不能满足风电齿轮箱精细化的设计需求,目前的做法是借助FEM计算,以第一级行星轮为例,建立第一级太阳轮及行星轮的FEM模型,如图17-1-38所示。

图17-1-38 齿轮FEM模型
对上述模型进行FEM求解,在齿顶沿齿宽方向提取变形数据,并将数据处理成如图17-1-39所示的形式。

图17-1-39 齿顶沿齿宽方向变形
结合图17-1-39可以对该轮齿齿顶变形进行评定,并据此制定合理的修形参数。同时,由于修形高度h的存在,使得修行以后渐开线长度将会变短,有可能造成啮合线长度不足的现象,因此需要确保修形后剩余啮合线长度大于一个基圆节距Pt,剩余啮合线长度L可以按照下式计算(参数见图17-1-40):

图17-1-40 齿顶修形宽度示意图
其中:
式中,ra为齿顶圆半径;rb为齿根圆半径:a为啮合中心距;、
为齿顶修形控制因子,通过控制
、
可实现三种不同的齿顶修形匹配模式。计算后,确定第一级行星轮齿顶修形参数如图17-1-41所示。

图17-1-41 第一级行星轮齿顶修形参数
②齿向修形 关于齿向修形的目的是消除轴系受弯后对齿轮啮合精度的影响,经验公式对于一般工业齿轮齿向修形是满足精度要求的,但如果需要进行更为精确的计算,则计算也可以采用解析算法或仿真法确定,使用仿真计算时,需要建立传动轴系的FEM模型,以第一级太阳轮轴为例,FEM模型如图17-1-42所示。

图17-1-42 第一级行星轮轴FEM模型
计算上述模型由于弯矩引起的绕变形曲线,并将挠曲线反映到齿面变形上,如图17-1-42所示。
将齿面宽度方向沿轴线节点的下挠值值提取出来并表述成如图17-1-44所示的形式。

图17-1-43 齿面沿轴线弯曲变形

图17-1-44 齿面沿轴线弯曲变形曲线
根据图17-1-44所示相对挠度可精确定制齿轮齿向修形参数,如图17-1-45所示。

图17-1-45 第一级太阳轮齿向修鼓参数
③螺旋角修形 轴系由于传递扭矩,反映到齿轮两侧产生相对扭转变形,同样以第一级太阳轮为例,通过FEM计算轴系扭转变形,并将扭转量折算到轴系齿轮两个端面的相对扭转角,从而确定最佳的螺旋角修形量,经FEM计算受载轮齿齿顶沿齿宽方向的扭转角如图17-1-46所示。

图17-1-46 接触齿齿顶的扭转变形曲线
从而确定其螺旋角修形参数如图17-1-47所示。

图17-1-47 第一级太阳轮螺旋角修形参数
2)重要零部件计算
行星架(图17-1-48)是风电齿轮传动系统的重要组件,行星架的刚度及强度对于均载以及整机性能影响较大,建立复杂结构件的弹性体力学模型困难十分大,因此常用的方法是应用FEM进行计算。

图17-1-48 行星架的三维图
对此三维结构,根据其定位形式,支撑形式,载荷以及工况制定合理的计算方案,进行FEM计算后,变形云图如图17-1-49所示:

图17-1-49 行星架变形云图
风电齿轮箱(图17-1-50)增速器箱体组件是整个齿轮箱的外壳,同时又是齿轮轴的支承体,其刚性对于齿轮啮合质量有很大影响,同时,刚性过大有可能导致箱体质量偏重,因此需要进行有针对性的计算及优化。

图17-1-50 箱体三维图
此结构除了需要确定内部轴承座的受力情况,还需根据其支撑情况确定连接处的外载荷,并制定的有效的边界约束条件,通过FEM计算后变形情况见图17-1-51。

图17-1-51 箱体变形云图
通过对计算结果进行分析,可以调整部件的局部结构,其目的有两个,调整结构的受力情况尽量使得结构应力均匀;实现轻量化设计,为整机设计提供条件,通常对于组件的优化不是一次完成的,需要经历多次优化才能形成一个比较满意的结果。图17-1-52所示为主法兰的拓扑优化过程。

图17-1-52 主法兰的拓扑优化过程
一个成熟的复杂结构件,通常是经过不断调整计算方案,调整边界条件,不断修正结构,从定性分析到逐渐定量计算的重复过程。同时,一个成熟合理的结构件,除了能够保证强度刚度需要之外,设计者应尽量保证结构受力均匀,并且具有良好的可加工可制造性,同时对于局部结构,经可能避免应力集中现象。
(10)传动系统的动力学分析
风电齿轮箱的动力学分析的主要目的是为了对齿轮箱的振动以及动力学响应等特性进行有针对性的预测,并通过修改设计的方法来避免齿轮箱各部件发生共振,以及削弱一些有害的动力学响应。风电齿轮箱的动力学分析一般包括以下两方面内容。
①齿轮箱结构模态分析—考虑实际约束条件和结构刚度矩阵的模态分析,得到齿轮箱的固有频率和在各阶频率下的振型,再比较轮毂中心输入转速的转频,即可在初始阶段判断齿轮箱是否会在输入转频激励下发生共振,从而能够据此模态计算结果对齿轮箱结构进行优化修改。使用专门的动力学计算软件进行模态计算,按照标准选取结构阻尼比5%,750kW风电齿轮箱的模态以及第一阶主振型如图17-1-53、图17-1-54所示。

图17-1-53 固有频率

图17-1-54 模态振型
②动力学响应计算—以外界输入的转频以及齿轮系统自身的啮频为激励,以刚度矩阵、固有频率以及约束为边界条件,计算箱体和轴件的动力学特性响应。系统的动力学特性包括速度变化、位移变化和加速度变化三项,通过响应曲线中出现的突变来判断该部件在哪阶固有频率下发生共振,同时还可以定性或定量地获知振动的幅值。图17-1-55是利用MAST计算得到的箱体响应图。

图17-1-55 动力学响应-加速度
图17-1-55说明:在外界激励接近26Hz时机体的加速度相应达到最大值,约为3.8m/s2,因此实际应用过程中需要尽力规避26Hz左右的外部激励,但这往往是齿轮箱设计的难点之一。需要特别指出的是,齿轮啮合过程中产生的传动误差是影响齿轮箱动力学响应的一个关键因素。因此应根据实际需要,分别考虑各种激励对齿轮箱的振动影响,最终使齿轮箱整体运行平稳。
(11)传动系统的可靠性计算
对于齿轮、轴承、轴等传动元件组成的传动系统,导致失效的可能性有多种,由于难以穷尽所有的可能性,将这些部件的失效形式以及机理可以简单归纳如下:轮齿折断;齿面点蚀;轴承受冲击载荷失效;轴承疲劳失效;轴的强度失效;轴的刚度失效;螺栓失效。
针对齿轮传动系统常见的失效形式,建立系统失效故障数模型(见图17-1-56),将零件和部件及系统之间的失效关系用一种图形逻辑表示,并建立确定性的逻辑算法,用以评价整个传动系统的可靠性。同时,将故障树中全部事件表示如表17-1-52所示。

图17-1-56 风电齿轮传动系统故障树
表17-1-52 风电齿轮传动系统故障树事件描述

如果假定同一类底事件具有近似相等的可靠度,则表17-1-52中的同类事件归纳为13类,分别定义为T1~T13,其所属关系及可靠度评定值见表17-1-53所示。
表17-1-53 底事件分类及其可靠度

对于上述模型,利用应力-强度干涉模型进行求解,这里,应力及强度是一个广义的概念,一般而言,将作用于零件上的物理量如应力、压力、位移、磨损等量统称为零件的广义应力,并用符号s表示;同时,将零件承受这种应力的能力统称为零件的广义强度,并用符号S表示,见图17-1-57。

图17-1-57 应力-强度干涉模型
图中应力和强度密度函数曲线均为以横坐标为渐近线,两条曲线中间出现的交错部分称为应力强度的“干涉区”,干涉区内强度大于应力的概率是零件可靠度的计算依据,按照蒙特卡洛统计法计算得到该750kW风电齿轮箱传动系统的可靠度为
R=P(z≥0)=95.23%
(12)风电齿轮箱噪声级别测试
1)执行标准
风电齿轮箱噪声级别测试可依据GB/T 16404 ISO/9614-1《Acoustics-Determination of sound power levels of noise sources using sound intensity,part1-Measurement at discrete points》以及ISO 8579-1《Acceptance code for gear units-Part1:Test code for airborne sound》进行。
2)齿轮箱噪声产生机理
齿轮箱由齿轮、传动轴、轴承、及箱体等零部件组成,它们在工作时将产生振动,同时向空气中辐射噪声。该噪声由两部分组成:一部分是箱体内零件产生的噪声通过箱体辐射到空气中形成的空气声;另一部分是箱体受到激励而产生振动向空气中辐射的固体声。空气声和固体声构成了齿轮箱的总噪声。
3)检测方案
根据GB/T 16404相关规定,由于试验台电机及陪试齿轮箱等噪声影响,应减小测量表面与声源表面之间的距离,采取测点距增速机机体表面距离d=0.35m。选用矩形包络面布置测点,各个面上分布4个采样点,共布置20个测点;齿轮箱测点布置图如图17-1-58所示:

图17-1-58 齿轮箱测点布置图
4)数据测试及处理
①法向声强级LIn,法向声强的对数量,Iref为参考声强,取10-12W/m2:
LIn=10 lg[|In|/Iref]
②1/3倍频带声强合成A计权声强,合成计算方法:
③平均声功率,单位时间内通过垂直于传声面积为S的平均声能量:
式中,Ii为i点平均声强:Si为测点对应面元面积:
④平均声功率级Lw,按标准测量的增速器平均声功率的对数量:
式中,W0为基准声功率,为10-12W。
测试设备采用AWA5633型声级计,声级计水平正对测量面。手持声级计身体距离声级计0.5m。各测点的原始数据见表17-1-54。
表17-1-54 噪声测试原始数据

考虑环境修正系数、背景噪声修正后,修正后的该齿轮箱声功率级为90.25 dB(A)。