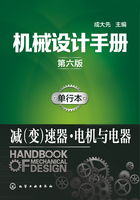
2 减速器设计举例
2.1 通用桥式起重机减速器设计
2.1.1 基本步骤
典型通用桥式起重机用减速器外形如图17-1-17所示。

图17-1-17 QJ3T通用桥式起重机用减速器
桥式起重机减速器设计步骤和其他通用减速器的设计步骤类似,主要分为如下几步:
①确定设计输入参数;
②确定载荷及工作级别;
③确定安装及装配形式;
④确定速比及功率;
⑤确定传动参数;
⑥承载能力计算;
⑦优化设计(主要指修形);
⑧维护保养。
本节以桥式起重机用主起升减速器为对象,介绍减速器选用、设计、计算及优化过程,仅供读者参考。
2.1.2 技术条件
通用桥式起重机减速器主要用于普通桥式起重机主副起升机构,其主要适应条件为:
①齿轮圆周速度不大于20m/s;
②高速轴转速不大于1500r/min;
③工作环境温度为-40~45℃;
④可以正反两向运转;
⑤减速器采用飞溅润滑;
⑥适用于钢丝绳下绳方向为内下绳。
根据用户提供的技术规格书,将总体技术条件汇总如表17-1-32所示。
表17-1-32 总体技术条件

2.1.3 确定工作级别
减速器设计过程中,正确地选择减速器的工作级别是前提。减速器工作级别实际上就是减速器用在起重机机构的工作级别,由以下一些因素决定。
(1)利用等级
利用等级按总使用寿命分为10级,见表17-1-33,表中总使用寿命为减速器在设计年限内处于运转的总小时数,并且结合使用频度以确定减速器的利用等级。
表17-1-33 机构的利用等级

经评定该起重机构应用于较频繁使用,因此其利用等级为T6。
(2)载荷状态
机构的载荷状态表明其受载的轻重程度,它可用载荷谱系列Km表示。
式中 Pi——机构在工作时间内所承受的各个不同载荷,Pi=P1,P2,P3,…,Pn;
Pmax——Pi中的最大值;
ti——机构承受各个不同载荷的持续时间,ti=t1,t2,t3,…,tn;
tT——所有不同载荷作用时间总和;
m——齿轮材料疲劳试验曲线指数,一般取3.0。
用户提供该起重机的简易载荷谱如表17-1-34所示:
表17-1-34 减速器简易载荷谱

根据上表计算得到该减速器载荷谱系数Km为
同时,机构载荷状态按名义载荷谱系数分为四级,见表17-1-35。
表17-1-35 载荷状态分级及其名义载荷谱系数

根据载荷谱系数,该减速器的载荷等级应为L2。
(3)确定工作级别
按机构的利用等级和载荷状态来确定机构的工作级别,共分8级(M1~M8),见表17-1-36。
表17-1-36 机构的工作级别

结合利用等级和载荷状态,评定该齿轮箱的工作级别为M6。
2.1.4 确定减速器速比
确定减速器速比按照下式计算:
D0=D+d
式中 D0——卷筒卷绕直径,mm;
d——钢丝绳直径,mm;
n0——电机转速,r/min;
u——滑轮组倍率;
vq——起升速度,m/s;
D——卷筒槽底直径,mm。
此条件下,减速机所需总速比为
2.1.5 确定电机功率
参照GB/T 3811—2008,起升机构所需电机功率按照下式计算:
式中 Pn——电机功率,kW;
PQ——起升载荷,N;
vq——起升速度,m/s;
η——起升机构传动总效率,采用闭式圆柱齿轮传动时,可初选η≈0.8~0.85。
按照上式,计算得到该起升机构的电机功率为
2.1.6 确定减速器功率
标准减速器有自己的选用方法,QJ型起重机用减速器用于起升机构的选用方法为
P0=1.12j-5Pn
式中 Pn——电机功率,kW;
P0——减速器额定功率,kW;
j——减速器工作级别,因是M6级,此处取j=6。
按照上式计算得到QJ型减速器的额定功率为
P0=1.12×37.7=42.2(kW)
确定该减速器的选用名义功率为43kW。
2.1.7 安装及装配形式
起重机用齿轮箱常用的安装方式可以是卧式、倾斜、立式安装使用,如图17-1-18所示:

图17-1-18 起重机用齿轮箱典型安装形式
根据用户要求,该减速器采用卧式安装,安装形式如图17-1-18所示,同时,QJ3T系列减速器具有六种装配形式,分别如图17-1-19所示。

图17-1-19 装配形式示意图
2.1.8 确定传动参数
根据上述设计参数及工况条件,按照三级传动进行传动方案设计,按照大约1.4倍递增关系分配三级中心距分别为250mm,355mm,500mm。然后对每一级进行详细设计,该减速器主要齿轮参数汇总如表17-1-37所示。
表17-1-37 传动参数表

根据上述传动参数,该减速器的传动方案如图17-1-20所示。

图17-1-20 减速器传动方案图
2.1.9 齿轮承载能力计算
我国现行的齿轮承载能力计算标准大多采用GB 3480或者1SO 6336,以末级传动大齿轮为例。
(1)接触疲劳强度计算
1)切向工作载荷Ft
切向工作载荷Ft按照下式计算:
式中 T——末级大齿轮名义转矩,N·mm;
d——末级大齿轮分度圆直径,mm;
P——末级大齿轮名义功率,kW;
n——末级大齿轮转速,r/min。
计算得到:
2)使用系数KA
使用系数KA根据原动机和工作机的工作特性选取,原动机为电动机,具有轻微冲击,工作机为桥式主起升,也是轻微冲击,按照推荐的使用系数选取方法,取KA=1.3。
3)动载系数KV
齿距偏差的极限偏差:
传动精度系数C:
取C=6,同时有
B=0.25(C-5.0)0.667=0.25
A=50+56×(1.0-B)=92
于是有
4)齿向载荷分布系数KHβ
由于采用硬齿面传动,取跑和系数xβ=0.85,啮合刚度系数cγ=20N/(mm·μm),同时,螺旋线总偏差Fβ为
加工、安装误差产生的啮合齿向误差分量fma为
fma=0.5Fβ=7.69(μm)
则啮合齿向载荷分布系数KHβ为
5)齿间载荷分布系数KHα
由于是6级硬齿面,按照推荐值取KHα=KFα=1.1。
6)单对齿啮合系数ZB、ZD
由于轴向重合度εβ>1,取ZB=ZD=1。
7)节点区域系数ZH
基圆螺旋角:βb=11267°,端面压力角αt=2041°,端面啮合角:。于是有
8)弹性系数ZE
根据齿轮材料,取弹性系数ZE=189.8MPa。
9)重合度系数Zε
10)螺旋角系数Zβ
11)寿命系数ZNT
按照10年设计寿命计算,考虑工作制后,末级大齿轮应力循环次数约为1.36×107次,渗碳钢寿命系数按下式计算:
12)润滑剂、速度、粗糙度系数(ZLZVZR)
按照持久长度以及加工方法,由于采用滚齿加磨齿加工,取ZLZVZR=0.92。
13)工作硬化系数ZW
由于热处理后齿面硬度达到(60±2)HRC,因此取ZW=1。
14)尺寸系数ZX
ZX=1.076-0.0109mn=0.9779
15)接触强度极限σHmin
18CrNiMo7-6经过渗碳淬火热处理后,其硬度可以达到(60±2)HRC,接触强度可达σHmin=1500MPa。
16)接触强度校核
接触强度计算安全系数SH:
满足用户提出的齿轮接触疲劳安全系数不小于1.2的要求。
(2)弯曲疲劳强度计算
1)齿向载荷分布系数KFβ
2)齿形系数YFa
采用标准刀具进行加工,αn=20°,hap/mn=1.0,hfp/mn=1.25,ρfp/mn=0.38。
当量齿数为zv=z/(cos2βbcosβ)=93.54,变位系数为-0.024,得YFa=2.14。
3)应力修正系数YSa
同上,当量齿数为zv=93.54,变位系数为-0.024,应力修正系数为YSa=1.67。
4)重合度系数Yε
当量齿轮的端面重合度为
重合度系数按下式计算:
5)螺旋角系数Yβ
螺旋角系数按照下式计算:
6)试验齿轮应力修正系数YST
一般情况下取YST=2.0。
7)寿命系数YNT
按照10年设计寿命计算,末级大齿轮的应力循环次数约为0.33×108次,按照下式计算寿命系数:
8)齿根圆角敏感系数YδrelT
齿根圆角敏感系数YδrelT近似取1。
9)齿根表面状况系数YRrelT
根据齿轮材料及表面粗糙度,近似取YRrelT=1.05。
10)尺寸系数YX
由于齿轮材料为渗碳淬火钢材,法向模数为9,按照图解法查得YX=1.0。
11)弯曲强度极限σFmin
18CrNiMo7-6经过渗碳淬火热处理后,其硬度可以达到(60±2)HRC,接触强度可达σFmin=500MPa。
12)弯曲强度校核
弯曲强度计算安全系数SF:
满足用户提出的齿轮弯曲疲劳安全系数不小于1.6的要求。同样其他两级传动的齿轮强度可以采用相同方法计算。
按照上述相同的方法,计算得到该减速器各级齿轮疲劳安全系数如表17-1-38所示。
表17-1-38 各级齿轮疲劳安全系数

2.1.10 齿轮修形计算
齿轮啮合过程中,由于加工误差及弹性变形使被动齿轮的实际基节大于主动齿轮的实际基节,从而产生边缘冲击,这种边缘效应会影响齿轮传动的平稳性,引起应力集中,并产生过大噪声。
(1)齿顶修形
对于线速度较低的传动齿轮,可以采用仅小齿轮修形的方式;当齿轮载荷以及线速度较大的齿轮,应该采取大、小齿轮均修形的方式,其中修形高度h可以采用推荐值:
h=0.4mn=3.6mm
大小齿轮的齿宽方向的修形量Δ1、Δ2可以按照以下经验公式计算:
推荐a=5~13mm,取b=0~8mm,一般情况下取中间值,另外Wt为单位齿宽载荷:
Wt=Ft/b=745N/mm
取a=8mm,取b=6mm,计算末级齿顶宽度修形量为
该级的齿顶修形参数可以表述如图17-1-21所示。

图17-1-21 第三级齿轮齿顶修形参数
(2)齿向修形 关于齿向修形计算也可以采用解析算法或仿真法确定,对于斜齿轮,齿宽范围内的最大相对弯曲变形可以通过下式计算:
式中 δb——弯曲变形量,mm;
Ψd——宽径比,Ψd=b/d1;
b——齿轮有效齿宽,mm;
d1——齿轮分度圆直径,mm;
Ki——考虑齿轮内孔影响的系数:
di——齿轮内孔直径,mm;
Kr——考虑径向力影响的系数:
Kr=1/cos2αt
αt——端面压力角;
η——轴承跨距和齿宽的比值,η=L/b;
L——轴承跨距,mm;
E——齿轮材料弹性模量,对于钢制材料可以取E=2.06×105MPa。
按照上述公式进行计算,将末级主动轮的齿向修形参数表示如图17-1-22所示。

图17-1-22 末级主动轮齿向修形参数
(3)螺旋角修形
轴系由于传递转矩,反映到齿轮两侧产生相对扭转变形,此变形使得齿轮螺旋角发生微变,假设载荷均匀分布,则齿宽范围内最大相对扭转变形通过下式计算:
式中,G为剪切模量,对于钢制材料齿轮,一般取G=7.95×104MPa。
根据上述计算得到末级主动齿轮的相对扭转变形量为
δt=0.0234mm
转换成齿宽上的扭转角为
结合扭转方向,该级主动齿轮的螺旋角修形参数表示如图17-1-23所示。

图17-1-23 末级主动轮螺旋角修形参数
同样,其他各级修形参数均可以类似计算获得。
2.1.11 轴系设计
轴分为光轴及齿轮轴,总体设计原则是:结构合理,避免应力集中,且具有足够强度(静强度及疲劳强度)。关于材料选取,光轴常用材料有45钢、35CrMo、42CrMo等;调质轴(齿轮轴),常见材料有42CrMo、34CrNiMo6、34CrNiMo等;对于硬质齿轮轴,常见材料有20CrMnMo、18CrNiMo7-6。从性能上说,Ni是在确保淬透性基础上同时提高韧性的最佳元素,而Mo是在确保淬透性基础上同时提高耐磨性的最佳元素。
通常,轴系设计常规步骤如下:
①根据总体布局,拟定轴线上零件位置以及装配方案;
②选择轴材料以及热处理方式;
③初步估算轴直径,进行轴结构设计,确保各个轴段的扭转以及弯曲强度,同时考虑键槽对强度的减弱作用;
④必要时校核轴刚度、临界转速及其扭振频率。
对于传动轴的安全系数,通常都是按照弯扭合成进行计算,其校核公式为
其中:
式中 Sp——考虑弯扭合成作用时的许用安全系数;
Sτ——只考虑扭转作用时的安全系数;
Sσ——只考虑弯曲作用时的安全系数;
εσ、ετ——弯曲以及扭转时的尺寸影响系数;
σ-1、τ-1——对称循环应力材料弯曲、扭转疲劳极限;
ψσ、ψτ——材料拉伸以及扭转的平均应力折算系数;
Kσ、Kτ——弯曲以及扭转时的有效应力集中系数;
σa、σm——弯曲应力的应力幅和平均应力,MPa;
τa、τm——扭转应力的应力幅和平均应力,MPa。
为了省略计算过程并减少重复计算,借助专业计算软件对各轴系进行计算,如以高速轴为例,建立该轴系的计算模型如图17-1-24所示。

图17-1-24 高速齿轮轴计算模型
上述模型不仅考虑了电机和齿轮的载荷,同时考虑了联轴器偏心形成的附加载荷。沿着轴线方向分别定义三个危险截面A—A(左轴承的右端面)、B—B(第一轴段轴肩处)、C—C(齿轮承载中心),按照弯扭合成法分别计算三个危险截面的疲劳强度以及静强度,计算结果如表17-1-39所示。
表17-1-39 高速轴安全系数

上述计算结果表明高速轴的疲劳强度以及静强度均具有足够的设计余量,同样的方法可以应用于其他轴系的强度校核。
2.1.12 轴承选用
QJ3T系列减速器已经成功使用多年,该系列减速器轴承通常使用球面滚子轴承,并且由于起重机用减速器通常是双向运行,因此定位方式采用单侧交叉定位方式,如图17-1-25所示。

图17-1-25 轴承选型及定位方式
关于其寿命计算,可以按照下式计算其基本额定寿命:
式中 n——轴承转速,r/min;
C——基本额定动载荷;
ε——寿命系数,球轴承ε=3,滚子轴承ε=10/3;
P——当量动载荷,N。
当量动载荷可以由轴承承受的径向载荷以及轴承载荷折算得到:
P1=XFr+YFa
系数X及Y分别表示对应轴承型号的径向载荷系数以及轴向载荷系数,可以根据轴承型号由轴承样本查取。按照上述方法,将各轴承的基本额定寿命见表17-1-40。
表17-1-40 轴承基本额定寿命

计算结果说明各轴承基本额定寿命均在3500h以上。