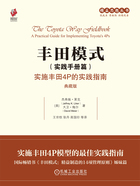
绘制现状价值流图时必须了解你的目标
在绘制现状价值流图时,必须按照头脑中对未来状况的展望对流程的现状进行评估。当你为了弄清楚当前流程中的主要障碍而实施精益时,必须明确自己想要取得的目标(这就是在第五篇中概述的解决问题的方法——明确定义问题,确定目标,找出实际与目标之间的差距)。你可能希望通过精益实现多个目标,下面列举了几个高层次的目标,这些目标都是精益价值流的典型特征。由于这是你首次尝试创建相互连接的价值流,你应该以下列条目为主要目标,在后续的活动中再关注更为具体的点的改进,持续地杜绝浪费情况:
1.灵活的流程,能够迅速应对客户不断变化的需求,尤其是产品种类的增加。这一流程能否随时生产出任一零部件?
2.较短的交付周期,缩短从客户下单到完成产品交付之间的时间间隔。
3.互相连接的流程(参见本书第5章),将无间断流程与拉动式材料流联结到一起。
4.每一个价值流在其内部都有独立的“流循环”,当流无法实现时,可以通过点来识别。这些“流循环”受当前流程的限制。
5.价值流中源自内部客户的简化信息流(下游流程)。
6.对客户需求清醒的认识(“客户的声音”)。在拉动制度环境里,客户(下一作业)决定完成什么及何时完成。客户的声音应提供:
a.需要的生产节拍(takt时间)。
b.需求量(数量)。
c.需要的型号组合。
d.需要的生产顺序。
7.每一个价值流及其内部的流循环都拥有一个“先导”作业步骤,所有其他作业的生产节拍都将由它决定。
记住这些特征之后,在绘制现状价值流图时,你就可以注意寻找与这些条件相悖的迹象,或者留意能够实现期望状态的地方。比如,在查看每一个流程时,你可以试着询问这样的问题:“这个流程的灵活性如何?能否迅速地(几分钟之内)从生产一种产品切换到生产另一种产品?”缺乏灵活性的迹象包括准备时间较长、生产批量较大等。同时,你有必要对前一流程能否生产出所需种类的产品进行评估。此外,在观察各个作业流程时,你还需要留意目前状况下用以弥补流程欠缺之处的方法。
存货是弥补灵活性不足的一种最常见的方法。在丰田看来,存货是流程中存在“弱点”的标志,它的出现是在提醒我们流程亟须加强。许多人将这一概念错误地解读为:流程中不应存在存货。在理想状态下,确实应该如此,但是实际上,如果没有存货,有些流程目前根本无法正常运转。丰田一直在朝着“即时生产”的理想目标努力,但同时,它始终坚持“战略性地利用存货以获得最佳的绩效”这一理念。对存货的战略性使用包括具体的规则和控制,以及在无间断流程中的位置要求。
小建议 存货的矛盾之处
有一种观点比较难以理解,即存货在精益体系中可能是有用的(至少短期看来是如此)。众所周知,存货过剩是八大类浪费之一,因此,我们的目标应该是消除库存才对。实际上,在流程实现无须库存的理想状态前,审慎地使用库存是有益的。有关八大类浪费的一个矛盾之处在于,人们倾向于将一种形式的浪费替换为另一种形式(就像换牌一样)。
问题的关键在于,思考浪费发生在何处、处于何种状态。换言之,浪费是出现在成品中,还是出现在在制品中?存货是否有助于流程实现更大的目标?你是否在尽量减少浪费?比较好的方式是,将存货向上游推,即推到价值流的起点处,并将存货应用到无法实现无间断价值流的情形中,比如,拥有多种产品和多个客户的流程以及灵活性差的流程。
在学习和绘制作业流程图时,必须查明存货的位置及种类(在制品、成品、购买的零部件和原材料)。每一种类型的存货通常是用来弥补某个具体的薄弱环节。
确定客户订单进入价值流的切入点(你计划在哪儿)。从客户订单的切入点开始,到产品到达价值流终点,需要多长时间?如果你正在“安排”多个切入点,请一并注明。多重安排点是“推动式”制造流程的标志之一。你有可能还会看到一些指标,显示不连续的流程,这时你需要留意存货在流程之前和之后的积累情况。它是不是被继续向前推动,而不顾下一流程是否需要?
观察一下由流程之外的人员(通常是来自生产控制部门的人员)安排的价值流中的流程,同时检查一下该流程是否使用了其他“非正式”的安排方法。监管员通常会随身携带一个笔记本,里面记载着根据其他监管员的要求做出的“真正的”日程安排。
误区 危险
当你看到价值流中存在的“问题”时,你可能会产生立刻去解决问题的冲动。但是,如果你急于着手去解决这些问题,那就偏离了主要目标——创建精益体系。尽管你终于花时间审查了你的流程,并从中发现了问题,但这并不代表你可以突然希望每个人都会立即采取行动,改正发现的问题。此刻,我们的主要目的是查明流程的现状,并明确需要采取哪些措施,才能使其在未来变得更好。
如果你发现有人使用未经指定的方法工作(如上文中提到的监管员使用“非正式”方法来安排流程),那么,你必须查明问题的真相。一般来说,员工不遵循规定的方法而采用其他方法工作,原因不外乎两点:①因为他们能这么做;②因为他们必须完成工作任务,但是现行的方法行不通(至少他们认为行不通)。
注意:任何出于安全问题的考虑或存在亟须解决的质量问题的情况除外。
在绘制现状流程图的过程中,你同样也在逐步了解当前流程的优劣。我们未来的目标之一就是要在价值流中创建一个相互连接的无间断流程。因此,我们首先需要观察每一个流程,确定其是不是“顺畅的”(flow through)流程,即能够毫无顾忌或限制、在任何时间生产任何产品。这些流程既不受较长的准备时间的限制,也没有其他妨碍其对各种型号、体积或订货量的具体处理能力的限制。顺畅流程的主要特征是“既来之,则处理之”的处理能力,而且工作任务也无须再按类别分批进行处理。比如,零部件冲洗就是一个很好的例子,你只需稍微修改一下操作参数,即可对所有的零部件进行相似的处理。
分析你的价值流,识别出标示某个具体零部件特征的作业流程。在价值流的开端部分,一个部件可以是许多成品部件的“基础模型”。比如,一个位于焊接部门的汽车车身可以变成一辆任何颜色的汽车,内饰也可以搭配不同色彩。但是,在车身被喷上了某一具体的颜色后,它就获得了颜色特征。在装配线上,每一步后续作业都可能将这一标志改变成某一具体的颜色,比如内部材质和可选配置套餐。创建部件标志的作业流程通常会收到有关生产什么产品的通知。依据实际情况,这些通知可能是来自外部的安排指示(来自生产控制部门),或者来自价值流内部的信号指示,如下游流程送还的看板。了解这些情况对于创建未来无间断价值流具有重要的意义。
图3-1中的未来价值流图展示了上文中提及的七个基本方面。让我们来了解一下基本的流程:生产控制部门收到客户的资料后,将相应数量的成品存货按照超市存货的方式存储起来,并为最终的顺畅流程创建了一份均衡化的生产计划表,这就是价值流中生产计划的一个点。这一流程先是从超市中拉动出材料,然后后退两个步骤,拉动一个先入先出的生产流程,并将其送至下一流程,最后通过这个流程拉动供应商。于是,这个价值流便具备了汇集于一点的、均衡化计划表的各种理想特征,并通过拉动式系统实现了从供应商到客户的无间断流程。
你的未来价值流图可能与书中的范例不尽相同。切忌用书中的范例与你的实际情况进行比较,并认为你无法实施流程中的某些方面。你应该力争使你的价值流取得最佳的效果,并创建一个与你的经营需求相匹配的流程。然而你大可放心,在某种程度上,你的流程也有可能实现上文中提到的七个根本方面。
1.灵活性。在这一价值流中,流程末端的成品超市用来改善灵活性。同时,它还被战略性地用来缩减从客户下单到完成交货的周期(对于客户需求量较大的产品,采用直接从存货中出货的方式)。如果你公司制造的产品种类繁多,在某些情况下,可能会用到存货超市(比如,对于需求量较大的产品)。请注意,在这个例子中,在编制均衡化生产计划表时,生产控制部门同时考虑了拥有成品存货的产品和客户的实际需求(参见本书第7章)。
2.较短的提前期。精益价值体系的一个主要特征是提前期非常短。请注意,在图3-2中,提前期是通过战略性地将零部件超市置于第一个流循环之后而得以缩短的。尽管存货被视为一种浪费,但是以这种方式来运用它,不仅改善了价值流的灵活性,同时还缩短了提前期。超市中的存货应维持在最低水平,且一旦价值流作业可以实现真正的无间断流程,便可以将存货清除。
3.互相连接的流程。请注意,这个例子中的存货超市通过拉动式制度将两个流程连接在一起。此外,两个不同流程之间圆形、方形和三角形的线路同样也表明了它们之间的连接。这表明该流程是一个“有序流程”——材料流按照相同的顺序从一个作业步骤流向另一个作业步骤,这种流程有时还被称为“先入先出”流程(FIFO)。我们将在本书第5章中对这些连接进行详细探讨。
4.流循环。存货超市界定了流循环的起点和终点,同时也是每个流循环的“客户”。流循环的目标始终是满足客户的需求。在流循环中,真正的“客户”是从存货超市中取货的作业步骤,而超市的消费代表的则是需求。如果你只有一个客户,或者是生产者生产的产品种类繁多,那么流循环中可能就不存在存货超市,在这种情况下,整个价值流从头到尾可能就是一个流循环。

图3-1 未来价值流图的基本示例

图3-2 未来价值流图(已完成元素界定)
5.简化的信息流。精益价值流的一个主要方面是其中的信息流可以被简化。信息可能来自外部,也可能来自内部。来自客户的外部信息流只能在一个点进入价值流,完成工作所需的所有其他信息均来自价值流内部。如果价值流中存在存货超市,那么存货超市就是信息的来源。如果使用的是“有序流程”,那么信息将会与产品一起流动。而“生产计划表”将由价值流中的某一个流程决定。从图3-2我们可以看出,有些机制用来传达“客户的声音”,客户提供的信息就是通过它来向流程传达何时需要做何事的指示。
6.对客户需求的认识。这一认识指的是在工作区中对实物的实际认识。它不是写在纸上的生产计划表。我们将在本书第5章对此进行详述。简而言之,它包括运用符号(看板)以及为各作业步骤之间实际界定的联系。
7.先导作业步骤。每一个价值流都必须拥有一个先导作业步骤(在《学习观察》一书中被称为pacemaker),而且,价值流内的每一个流循环同样必须拥有一个先导作业步骤。价值流的先导作业步骤最终将为所有作业步骤定速,但是存货超市是流循环的分配者,因此需要单独的先导作业步骤。