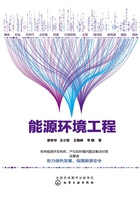
2.4.2 碎煤的沸腾燃烧
碎煤是指粒径较小(一般小于10mm)的煤粒或煤屑,其燃烧方式主要是沸腾燃烧,相应的燃烧装置叫沸腾炉。
沸腾燃烧相当于在火床中当火床通风速度达到煤粒沉降速度时的临界状态下的燃烧,煤粒由气力系统送入沸腾床中,燃烧所需空气经布风板孔以高速喷向煤层,使煤粒失去稳定而在煤层中作强烈的上下翻腾运动,因其颇类似沸腾状态,故称为沸腾燃烧。图2-8所示为沸腾燃烧的原理。由于煤粒和空气进行剧烈的搅拌和混合,燃烧过程十分强烈,燃料燃尽率很高(一般可达到96%~98%以上),所以沸腾燃烧能有效地燃用多种燃料,如无烟煤、烟煤、褐煤及油页岩等多种固体燃料。但由此而由烟气带出的飞灰量也较大,一般需经二级除尘后才能达到排放标准。
为防止沸腾层内灰渣结块破坏燃烧过程,通常在沸腾床内设置埋管受热面,使床内温度维持在800~900℃之间。这些受热面由于受到强烈翻腾煤粒的冲刷,使热阻的层流边界层常遭破坏,故受热面可达到很高的传热系数[可达250~350W/(m2·℃)]。因此,较小的受热面积即可传递大量的燃烧放热量。沸腾燃烧属低温燃烧,在800~900℃的床层温度下,对脱硫化学反应很有利,因此,常随燃料加入一定数量的CaCO3及MgCO3作为脱硫剂。据研究,在Ca/S≥2的条件下,可使燃料中大部分的硫(80%~90%)被化合成CaSO4炉渣残留下来,从而防止有害气体SOx对大气的污染。由于低温燃烧,排气中的有害成分NOx也大为降低。

图2-8 沸腾燃烧原理
1—燃料管;2—排灰管;3—进气管;4—布风板;5—混合器
固体燃料的沸腾燃烧,是介于层燃燃烧和悬浮燃烧之间的一种燃烧方式,它是利用空气动力使煤在沸腾状态下完成传热、传质和燃烧反应。沸腾燃烧法所使用的煤的粒度一般在10mm以下,大部分是0.2~3mm的碎屑。沸腾燃烧炉具有如下优点。
(1)燃烧稳定,对燃料适应性大
沸腾炉采用颗粒较小的煤末工作,燃烧面积很大。且颗粒在炉内停留时间长,炉内蓄热量大,混合又十分强烈。因此着火和燃烧都很稳定,可以采用含灰量多、水分大、挥发分少的劣质燃料来工作。又由于沸腾炉内温度较低,有利于灰熔点低、含碱量高的燃料工作。所以这种燃烧方式可以采用广泛的燃料品种,燃料的适应性大。
(2)沸腾床内传热强烈,可节省受热面钢材
沸腾床内的受热面,由于颗粒上下翻滚,因此传热性能很好,传热系数通常可达250~350W/(m2·K)。这一数值比一般对流传热系数大3~4倍,因而可大大节省受热面耗用的钢材。
(3)污染物排放较少,对环境保护有利
沸腾床内维持的温度较低,因此燃烧生成的NOx较少,可以大大减轻氮氧化物对大气的污染。
(4)容积热强度大,锅炉体积小
沸腾炉内燃烧强度很大,炉膛的容积热强度可达1750~2080kW/m3,约为普通煤粉炉的5倍,再加上炉内传热系数又大,因此沸腾炉的体积较小。与煤粉炉相比体积约可减小2/3,造价可降低15%左右。
(5)灰渣具有“低温烧透”的特点
灰渣不会软化和黏结,可用作水泥等建筑材料,也可作沥青和塑料的填料,或进行其他综合利用。由于沸腾炉能烧各种燃料,解决了劣质煤的利用问题,并给大量煤矸石的利用找到了出路,对实现煤炭资源的合理利用问题有重要意义。然而,沸腾炉在运行过程中也存在不少问题,主要包括:
① 飞灰量大,飞灰中含碳量高,因而锅炉热效率低(60%~75%)。
② 炉内受热面和炉墙磨损比较严重,沸腾层中埋管一般一年左右就得更换。
③ 烟尘排放浓度大,一般必须二级除尘。
④ 运行中燃料需破碎至10mm以下,且送风需要压力高(5886~7848Pa)的鼓风机,因而耗电量大。
⑤ 加石灰石脱硫时,石灰石的钙利用率低,为达到较高的脱硫效率,需用大量的石灰石。
上述问题严重影响沸腾炉的进一步发展和应用,但随着沸腾燃烧技术的进一步发展,这些问题不断地得到了改善和解决,由此发展起来的流化床燃烧技术已在实际中得到了广泛应用。