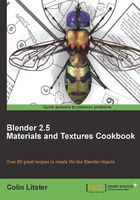
In this chapter, we will cover:
- Creating a slate roof node material that repeats but with ultimate variety
- Using a tileable texture to add complexity to a surface
- Warping a texture to disguise seams in a repeated texture
- Adding weathering by copying and reusing textures
- Combining materials using nodes
- Creating metals
- Creating a realistic copper material
- Using image maps to suggest man-made metal materials
- Using specular maps to add age and variety to man-made surface materials
- Adding oxidization weathering to our copper material
- Adding grime and artistic interest to our copper material
- Creating a road or path material that never repeats
- Repeating a tiled texture to duplicated objects
- Deforming materials and textures in Blender
Man-made materials and textures are probably the most used and applied in any 3D environment. The need to simulate created and manufactured objects is therefore an important skill to learn and apply within Blender. Fortunately, the techniques necessary to simulate man-made surfaces are no more difficult than creating natural surfaces.
Blender offers many tools to aid the process of creating man-made materials. Its material system makes it easy to manipulate textures and apply them to a surface, reproducing properties such as:
- Color changes, due to oxidization, or other environment-specific interaction
- Scratches, due to wear and tear, specifically on those areas of an object that are more frequently handled or interact with other objects
- Dirt and grime that collect on man-made surfaces like rust, dust in any gullies, or vegetation that will grow on man-made materials if exposed to air and moisture for any length of time.
All these things will place our object in the context of its man-made origins. Identifying these attributes and reproducing them within a Blender material will sell your material solution as being man made.
So, even though a man-made material may be fashioned out of natural substances, its surface, as well as its shape, will provide the clues as to its man-made origins.
The things that differentiate such surfaces from natural counterparts often describe the process of manufacture and the way we interact with them. So, a man-made surface will have been :
- Moulded – beaten, pressed, folded, and cut, each of which will have an effect on the surface.
- Cast – clay and metals are often cast to produce new shapes. These castings will produce new surface bumps specific to the casting method. Cast iron can have a lovely granulated surface because sand is used as the casting mould.
- Coated – many man-made materials have to be coated to protect them from the elements. Paint, anodizing, and other coating methods may change the appearance of the surface but the underlying substance can affect the bump and sometimes the coverage of the coating. So, rust and other oxidization on metals can eventually wear through the coating.
- Polished – man-made objects are often polished in some way, either by coating with varnishes and polishes, or by their designed interaction with other items. So, a cast metal cylinder may be rough on the outside, but cut accurately in its center, to allow a piston to move, with the actions of the piston continually polishing the bore of the cylinder.
- Marked – Human handling, or the environment-specific location, will lead to handling marks or task-specific grime. So, man-made materials will have different specularity levels across its surface, particularly where human hands have been in contact. Also, exposed edges of man-made materials often wear more because of their vulnerability to human interaction.
All these things should set a man-made surface into context. Recognizing these surface attributes and finding ways to simulate them within Blender will improve your chances of convincing the viewer that what they see is actually meant to represent a manufactured object.
That doesn't mean you have to create absolute reality in your man-made material designs. Sometimes, you can fake a material by giving just enough surface information to fool the eye. This is valuable because we may not be able to use enormous image maps, with their inherent memory-hogging disadvantages, with every man-made material simulation. So, keeping things simple will help you as a designer, as well as improve render times, the size of your blendfiles, and the complexity of models. This is particularly important when you consider how complex you wish to make the mesh representing the man-made object.
A good material can add detail to a simple mesh with little of the memory overheads associated with millions of vertices. In fact, a cube made from 8 vertices will look exactly the same as one with 87,848. However, the first will render in 4.69 sec, on my computer, while the second will take 10.05 sec. That's twice as long and with the other disadvantages of a large memory overhead that will slow your computer to a crawl. Therefore, consider adding just structural detail via the Blender material rather than trying to model all the dents, curves, indentations, and other complexities of the real surface.
As a 3D designer, you will also be expected to create visually interesting surfaces. Sometimes, it will be better to emphasize surface attributes to make the render more exciting. Just as with natural material simulation, our task is to provide the viewer with the essence of the surface we are trying to duplicate but also add that magic flare that will transform our man-made material simulation to the next level.
Note
Several of the recipes in this chapter require the use of a paint package. You will struggle if you do not have access to one. I can recommend GIMP, which is another free open source package like Blender. It is available for any of the major computer platforms from: http://www.gimp.org/downloads/