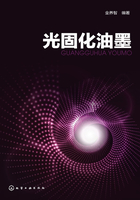
3.4 UV胶印油墨
胶印又叫平版印刷,是在印刷领域内应用最广泛的一种印刷方法。胶印印版的图文部分和非图文部分基本上处于同一平面,仅有稍许高低之差,利用油水相斥的原理印刷,图文部分是憎水性的(亲油墨),非图文部分是亲水性的(斥油墨)。印刷时先用润版液润湿非图文部分,图文部分是斥润版液的;再由墨辊传递油墨,图文部分接受油墨,非图文部分斥油墨;图文部分油墨再转移到橡胶辊筒,然后传给承印物,是间接印刷。胶印印刷过程如图3-10所示。

图3-10 胶印印刷过程示意图
3.4.1 胶印印刷的制版
胶印使用的印版为预涂感光平版(presensitized plate,PS版),是在铝基版上预先涂覆感光层,加工后储备,随时用于晒版的胶印版。PS版有阳图型PS版和阴图型PS版两种。20世纪80年代开发出数字化制版技术——计算机直接制版(computer to plate,CTP)技术,代表了印刷技术最新的发展方问,进入21世纪,CTP技术日渐成熟,CTP设备和版材不断开发和获得进展,正在成为胶印的主流产品。
(1)阳图PS版
阳图PS版是在经表面处理的铝基材上涂布光降解型邻重氮萘醌类感光剂与线型酚醛树脂组成的感光树脂层,经干燥制成。
阳图PS版的制版过程:
UV曝光→显影→干燥→修版→印版
阳图PS版使用时,将阳图底片与阳图PS版真空贴合,用金属卤素灯(如碘镓灯)或中压汞灯曝光,在紫外光照射下,重氮基发生分解,析出氮气,同时发生分子内重排变为烯酮,在水存在下烯酮水解变为羧基,因为感光部分产生了羧基,用碱性显影液如硅酸钠、磷酸钠、碳酸钠或有机胺等进行显影而除去,露出的铝基材亲水。不感光部分形成图文亲油墨,得到阳图。版面经除脏、修版、干燥,即制成印版。有时为了提高耐印力,还可采用高温烤版。
(2)阴图PS版
阴图PS版是在经表面处理的铝基材上涂布光聚合型感光性树脂,如重氮树脂与碱溶性树脂体系、带叠氮基的高分子体系和带肉桂酸基团的高分子体系,它们的感光度比阳图PS版高,但有一部分是溶剂显影,成本高,对人体有害,也污染环境。
阴图PS版的制版过程:
UV曝光→显影→干燥→修版→印版
阴图PS版使用时,将阴图底片与阴图PS版真空贴合,用金属卤素灯(如碘镓灯)或中压汞灯曝光,在紫外线照射下,见光部分发生聚合交联,形成的图文部分亲油墨。对于不见光部分,有的体系用稀碱液如碳酸钠显影除去,有的体系要用溶剂显影除去,露出的铝基材亲水,得到阴图。版面经除脏、修版、干燥,即制成印版。
(3)CTP版
CTP技术是使用数字化数据通过激光制版机将图像和文字直接复制到印刷版上的技术。CTP制版工艺与传统胶印制版工艺相比,不需要银盐分色胶片,还可省去多道制版工序,如图3-11所示。

图3-11 CTP工艺和传统胶印制版工艺比较
CTP制版系统因结构不同,所用光源不同,所用的CTP版材也不同。目前主要有紫激光CTP版、热敏CTP版和UV-CTP版,它们的版材结构、成像机理和性能各不相同,各有特点(见表3-30)。
表3-30 常见三种CTP版材性能比较

3.4.2 胶印印刷
胶印的主要特点如下。
①油墨层厚度很薄,一般胶印油墨单色厚度在2μm左右。
②由于墨辊和水辊交替与印版接触,故对油墨印刷适性要求极高,同时要防止油墨发生乳化。
③胶印的印刷速度快,一般在100~400m/min。
④胶印油墨黏度高,颜料浓度高,着色力也高。
⑤胶印是间接印刷,是由有弹性的橡胶辊转印给承印物的,所以印刷压力比较小且均匀,套印精度高,图文再现性好,网点清晰,层次丰满。
传统的胶印油墨是以松香改性酚醛树脂等合成树脂为连接料的溶剂型油墨,污染环境,采用UV胶印油墨后,则使胶印印刷有了新的进展。
(1)改善了普通胶印工艺
①胶印中使用UV油墨,印刷品在到达收纸部分已经固化,可以免去喷粉,既利于印刷环境的清洁,保护操作人员的健康,也避免了由于喷粉而给印后加工所带来的麻烦,如对上光、覆膜效果的影响,并可进行连续加工。不仅改善了作业环境,而且提高了生产效率,又缩短了交货时间。
②UV油墨经UV光源照射才固化,未照射前在墨罐中不结皮,在印机或版上也不会干结,因此,胶印机停机不用清洗墨罐和胶辊,解决了胶印机停机时的后顾之忧,减少了油墨的浪费,节省了清洗时间。
③固化装置简单、易维修,不需要红外干燥装置那样的烘道,即便加上与之相关的设备,占地面积仍然比普通的红外干燥设备的占地面积小很多。
④紫外线固化设备能使UV油墨低温下快速固化,它的能耗比传统油墨印刷通过热风干燥或红外烘干的方式进行干燥所消耗的能量低得多。
(2)使胶印适用于多种承印材料,拓宽了胶印的应用范围
①复合纸类承印材料印刷。复合纸是由两种或两种以上的具有不同性能的纸或其他材料结合在一起组成的纸材,像日常生活中常见的牛奶、烟、酒的外包装盒大多采用复合纸制成。复合纸材料用普通油墨印刷存在附着力、耐摩擦性及干燥性差等问题。UV油墨中的光敏剂在UV的照射下,树脂中的不饱和键打开,相互交联形成网状结构,极大地提高了墨层表面的物理性能,从根本上解决了以上的一系列问题。
②非吸收性材料印刷。如聚乙烯薄膜、聚氯乙烯薄膜、聚丙烯薄膜、金属箔及非吸收性的特殊材料等。这些承印材料若采用普通溶剂型油墨印刷,除需要一定的干燥时间外,通常还需要采用喷粉、晾架装置或在油墨中掺加其他助剂等处理手段,而UV油墨固化时无渗透,完全摆脱了普通油墨干燥慢的困扰。此外,UV油墨可以提高墨层表面的物理性能,并可采用胶印UV油墨印刷细砂、金、银等,而普通胶印很难实现印刷。
③金属材料印刷。在金属材料表面采用UV油墨印刷时,可以缩短固化过程和简化原有的固化装置。同时,UV油墨表层良好的固化性和结膜性不仅可以改善印后加工特性,也提高了产品的外观质量。
(3)UV胶印具有优秀的印刷效果
胶印多用于精细产品印刷,UV胶印油墨印后立即固化干燥,油墨不渗入承印物内,故色彩更鲜艳,清晰度更高,大大提高了印刷品色彩饱和度,并且可减少细小网点的损失,提高套色叠印的油墨转移率。此外UV胶印印品在表面质地、保护性、耐磨性和生产效率等方面具有传统胶印印品所无法比拟的优势,使印刷品具有耐用、防擦伤和划痕等优点,同时还具有抗化学药品性和耐腐蚀性。
(4)UV胶印属于绿色环保印刷
环境问题是促使UV油墨大量使用的主要原因。绝大多数的油墨用户选用UV印刷技术的主要原因是UV油墨的应用符合环保法规。
①无溶剂挥发。UV印刷几乎没有挥发性有机物(VOC)的排放,解决了溶剂型油墨干燥过程中的环境污染问题。
②节省能源。传统溶剂型的油墨中有相当比例的溶剂在结膜过程中挥发掉了。因此,如果在同样面积、同样膜层厚度的印刷区域下做比较,显然溶剂型油墨的能耗量要大得多。
(5)UV胶印扩大了胶印在特殊印刷领域的应用
随着胶印技术的应用不断成熟,许多设备制造厂商推出了各种型号的UV胶印机。利用这种胶印机可以进行简单、高品质的光栅立体印刷作业。由此,立体印刷可以大批量地进行生产而且产品的质量得到进一步的提高,拓宽了胶印在特殊印刷领域的应用。
3.4.3 UV胶印油墨的制备
根据胶印的特点,UV胶印油墨配方设计应考虑低聚物和活性稀释剂要有较好的抗水性能,在印刷中与墨辊和水辊交替接触时,不发生乳化现象。UV胶印油墨中颜料浓度高,为了更好地分散颜料,常选用对颜料分散性能好的聚酯丙烯酸酯作为主体树脂成分;胶印印刷速度快,一般在100~400m/min,因此UV胶印油墨配方设计必须首先考虑油墨的光固化速度要符合胶印机车速要求。
3.4.3.1 选用光固化速度快的低聚物、活性稀释剂和光引发剂
低聚物和活性稀释剂要选用固化速率快、官能度高的丙烯酸树脂和活性稀释剂,常用于UV胶印油墨的低聚物见表3-31~表3-34,常用于UV胶印油墨的活性稀释剂见表3-35。
表3-31 湛新公司推荐用于UV胶印油墨的低聚物

表3-32 沙多玛公司推荐用于UV胶印油墨的低聚物

表3-33 沙多玛公司推荐用于UV胶印油墨的新低聚物

表3-34 国内公司推荐用于UV胶印油墨的低聚物

表3-35 沙多玛公司推荐用于UV胶印油墨的活性稀释剂

UV胶印油墨所用的光引发剂通常也是以ITX和907复合使用为主,对红、黄两色油墨可加651,但ITX和907有毒性,欧美发达国家已禁止使用,ITX可用DETX来代替,大分子ITX(Omnipol TX,北京英力公司生产)也可代替ITX;907可用UV6901(长沙新宇公司生产)、Doublecure 3907(台湾双键公司生产)来代替。黑色油墨则以369为主,配合ITX或DETX使用,白色油墨则以TPO和819为主,与184或MBF配合使用。UV胶印油墨的光引发剂用量比较大,一般都需6%或更多一些。为了提高表面固化速率,往往还需适当加入少量叔胺,如EDAB等。有时为了提高光固化速率,可添加适量的TPO或819。
UV胶印油墨配方设计中还可考虑以下组分。
(1)使用大分子光引发剂
上述介绍的光引发剂均为低分子量有机化合物,其光裂解产物分子量更小,容易发生迁移,有些有气味,有些还有一定毒性,ITX、907和BP等光引发剂欧盟已明确规定不能用于食品、药品包装印刷油墨中。为了适应安全和环保要求,使用低迁移性、低气味、低毒的光引发剂已经成为刻不容缓的事情。目前的发展趋势是使用将小分子光引发剂键合在高分子链上的大分子光引发剂或在小分子光引发剂中引入可聚合基团的聚合型光引发剂。大分子光引发剂由于具有较大的分子量,并含有可参与自由基反应的基团,有效降低了气味,改善迁移性,解决了残留光引发剂和光解产物的毒性问题。同时一个大分子光引发剂可形成多个自由基,局部自由基浓度可达到较高水平,有利于提高UV油墨的光固化速率。另外大分子光引发剂多以黏稠液体的形式存在,可大大改善与预聚物和单体的相容性。已经产业化的大分子光引发剂见表3-36。
表3-36 已产业化的大分子光引发剂

(2)使用低皮肤刺激性活性稀释剂
在UV油墨配方中所使用的丙烯酸酯类活性稀释剂有些对皮肤具有一定的刺激性,在UV油墨的生产和印刷过程中,一线的生产操作人员都会因为直接接触到丙烯酸酯类活性稀释剂而出现皮肤过敏的症状,所以为改善生产和印刷作业环境,提高油墨的生产安全性,希望使用皮肤刺激性指数(PII)在3以下(最好小于2)、挥发性低、气味小的活性稀释剂来改善UV油墨对皮肤的刺激性。
目前,降低活性稀释剂的皮肤刺激性指数PII值的方法主要有以下几种:
①活性稀释剂的烷氧化(乙氧化、丙氧化),增加活性稀释剂分子中烷氧基的数量和含量;
②加大丙烯酸酯活性稀释剂的分子量;
③用己内酯对活性稀释剂进行加成反应。
低皮肤刺激性的活性稀释性见表3-37。
表3-37 低皮肤刺激性的活性稀释剂

3.4.3.2 改善UV胶印油墨的流变性能和印刷适性
(1)颜料润湿性
UV胶印油墨的连接料主要由较高极性的低聚物和活性稀释剂组成,应用于UV胶印油墨中的颜料大多为极性较低的有机颜料,这些高极性的低聚物体系对低极性的有机颜料粒子表面的亲和性是比较差的,难以提供良好的颜料润湿性。同时,UV胶印油墨连接料所使用的主体丙烯酸酯低聚物分子量较低,通常为1000~2000(而传统胶印油墨所使用的松香改性酚醛树脂分子量为20000~50000)。总之,与传统胶印油墨相比,UV胶印油墨的树脂和连接料体系具有低分子量、高极性的特征,不能提供令人满意的颜料润湿性和分散稳定性。
为改善UV胶印油墨的颜料润湿性和分散性,提高生产效率,首先要选择合适的主体低聚物树脂。脂肪酸改性丙烯酸酯低聚物因具有较高的分子量、低极性而具有良好的颜料润湿性,特别适合颜料含量较高的胶印油墨体系。但由于部分丙烯酸官能团被脂肪酸所取代,脂肪酸改性丙烯酸酯的反应活性差、Tg低,会影响油墨的固化速率和墨膜的物理性能,通常必须和低黏度、高官能度的低聚物配合使用。选择合适的颜料也是改善油墨分散性能的关键因素之一,但是除UV油墨专用炭黑以外,极少有专门与UV胶印油墨配套使用的有机颜料,有机颜料的最终确定只能依靠大量的实验来进行。不过UV体系颜料选择有一个原则,就是在UV胶印油墨中适用的颜料应该是具有一定极性的。
(2)水墨平衡性能
在实际印刷过程中,UV胶印油墨对润版液水量的宽容度小,水墨平衡难控制,难以达到传统胶印油墨的印刷适性。导致UV胶印油墨水墨平衡性能差的原因主要有以下两方面,首先是UV胶印油墨中所使用的丙烯酸酯低聚物和活性稀释剂通常带有羟基、羧基和氨基等高极性基团,对润版液具有较强的亲和性,与极性小的油性连接料相比,前者的乳化可能性更大。其次是UV胶印油墨的印刷基材主要是以合成纸、金银卡纸和塑料等非吸收性材料为主,对润版液的吸收性差,这给印刷中水墨平衡又增添了更多可变因素。经验显示,使用残留羟基数值高和极性大的反应性低聚物(含调节用树脂、活性稀释剂、助剂)时,必须十分慎重。
主体低聚物的选择是改善UV胶印油墨水墨平衡性能的关键。由于环氧丙烯酸酯和聚氨酯丙烯酸酯预聚物的分子链上含有羟基、氨基等官能团,具有较强的亲水性,而损失油墨的抗水性,所以从改善油墨的水墨平衡性能角度来看,聚酯丙烯酸酯具有更好的抗水性,成为最佳的选择。目前从油墨性能方面看,UV胶印油墨体系大多以聚酯丙烯酸酯作为主体树脂,改善油墨的水墨平衡性能也是主要选择依据之一。但是聚酯丙烯酸酯低聚物在硬度、耐摩擦性和溶剂耐抗性方面还有待进一步改善。另外,在保持油墨体系黏性相近的条件下,采用更高分子量的丙烯酸酯低聚物则可以提高油墨的抗乳化性能,但是这种情况是在高分子量树脂在油墨的配方中达到一定的比例时才具有的,可能是由于高分子树脂之间通过相互缠结可以形成更大的物理网状结构,将有效阻碍水分子向油墨体系内部渗透,从而改善油墨的乳化性能。然而,丙烯酸酯低聚物的高分子量化是以降低官能度、损失固化速度为代价的,这就需要在设计油墨配方时进行综合考虑,以弥补为改善油墨的水墨平衡性能而导致其他性能恶化的损失。
环氧丙烯酸酯类低聚物是影响油墨乳化率的主要因素。因此,在保证固化速度和油墨黏度的前提下,应控制环氧丙烯酸酯类低聚物的用量,使UV胶印油墨能保持较强的斥水性,以保证在实际印刷生产中具有良好的印刷适性。
(3)降低飞墨现象
UV胶印油墨和传统胶印油墨相比在流变性能方面存在显著差异。首先,丙烯酸酯低聚物的颜料润湿性差,使UV胶印油墨在低剪切速度下表现出更强的结构,并对油墨在印刷机墨槽中的流动产生不利影响。其次,丙烯酸酯低聚物具有特殊流变性能和低分子量的特征,导致UV胶印油墨内聚力差,对温度变化敏感,表现出高黏性、低黏度和丝头长的特征。在高速印刷条件下,由于油墨体系的黏弹性不足,容易出现飞墨现象。如果为了顾全油墨的流动性和易分散性而选用易分散或高流动性的颜料,则此类问题会更加突出。
目前大多采用添加非反应型助剂的方法来改善体系的抗流变性能,提高UV胶印油墨抗飞墨性能。通常在油墨配方中添加气相SiO2、滑石粉、有机膨润土和有机硅树脂等具有一定增稠作用、可提高触变性的填充料,通过增加体系的内聚力和黏弹性来防止飞墨。但这些助剂的效果很有限,无法从根本上解决问题,而且可能对油墨的光泽度、附着力等性能产生不良影响。
改善低聚物树脂自身的流变性能是解决UV胶印油墨流变问题的最有效办法。从理论上看,在油墨配方中引入100%反应活性、具有流变性控制效果的低聚物树脂,不但将改善油墨的印刷适性,而且将改善油墨的最终固化成膜性能。
3.4.3.3 提高对基材的附着力
由于UV胶印油墨有瞬间固化和低温固化的特性,不仅在普通的纸张上可以使用,还可以应用于合成纸、金属覆膜纸、PVC、PC等各种非吸收性纸张和塑料。然而,在自由基聚合时,单体或低聚物间由固化前的范德华力作用的距离变为固化后的共价键作用的距离,两者之间距离缩小,因此体积收缩明显。加之固化时间极短,墨层的内部残存着很大的应力,因此与一般的溶剂型油墨相比,UV胶印油墨有附着力变差的趋势。
目前,对于一些特殊的塑料基材(如PE、PP和部分PET)UV胶印油墨不能提供良好的附着力,主要是由于这类材料具有活性稀释剂无法溶胀、表面极性低的特征,已固化墨膜与基材之间无法形成有效的作用力,导致附着力差。解决UV胶印油墨对这些塑料的附着问题是行业中难以克服的技术难题。根据实践经验,解决UV胶印油墨对困难基材的附着问题,通常从以下几方面着手:①增加低表面张力的活性稀释剂,改善油墨对基材的润湿性。②选用低官能度的活性稀释剂和低聚物,以减小油墨的应力和体积收缩。③选择高分子量、低Tg的低聚物。④使用特殊官能团改性的低聚物例如氯化聚酯丙烯酸酯等。⑤添加附着力促进剂。
但是这样处理常会导致油墨的固化性能变差、印刷适性有恶化的趋势。从应用状况来看,要使UV胶印油墨对所有基材都具有良好的附着性能是十分困难的,所以在改善油墨性能的同时,也必须对基材进行表面预处理(如电晕处理、火焰处理)或做增黏底涂层等,以改善基材的表面性能。总之,必须结合印刷工艺共同解决UV胶印油墨对于基材附着困难的问题。
使用UV胶印油墨还需注意下列问题。
(1)印版
胶印印刷时可使用阳图型PS版和阴图型PS版。如果是阳图型PS版,由于活性稀释剂和光引发剂能分解普通PS版的网点,造成印版耐印力下降,故必须使用UV油墨专用的阳图型PS版。如果用一般的阳图型PS版,需要进行烤版处理,即按照常规方法晒制的普通PS版,需要烤版10~15min(温度250℃)。CTP版也需要烤版10~15min(温度250℃)。
(2)胶辊、橡皮布
要使用UV专用胶辊,采用油性油墨和UV油墨兼用型胶辊其效果也可以。橡皮布选用一般油性油墨用、UV油墨用的橡皮布都可以,但由于UV油墨中的活性稀释剂会在印刷过程中对普通胶辊和橡皮布进行浸透,一方面造成油墨中活性稀释剂的减少,破坏了油墨的流动性;另一方面造成对胶辊和橡皮布的腐蚀,短期会导致胶辊和橡皮布表面膨胀变形及表面的玻璃化,长期印刷时胶辊和橡皮布表面会局部脱皮或产生裂痕。所以通常选用三元乙丙橡胶(EPDM橡胶)或硅橡胶制成的橡胶辊,硬度最好在肖氏40SH以上。选用UV专用橡皮布,该类橡皮布混合料中加入抗UV树脂成分,可耐UV照射,橡皮布不易粉化。或者选用UV自粘式橡皮布,该类橡皮布也含抗UV树脂成分,用于UV印刷时,寿命得以延长。
(3)分散和研磨
UV胶印油墨所用颜料量在各种油墨中最大,一般在15%~21%,所以分散、研磨非常重要,通常都先用分散树脂、活性稀释剂、润湿分散剂和颜料在砂磨机上分散、研磨,制成色浆,再将其余组分混匀后,用三辊机研磨制成油墨。
3.4.4 无水胶印
无水胶印是一种平凹版印刷技术,印刷时不使用水或传统润版液,而是采用具有不亲墨的硅橡胶表面的印版、特殊油墨和一套控温系统。与传统胶印技术相比,无水胶印有优异的印刷效果、更高的印刷效率及环保等优点。
3.4.4.1 无水胶印技术的特点
(1)印刷效果好
①色彩饱和度高。印刷中没有水的介入,所印图像因油墨未被稀释和乳化而更光亮、鲜艳,印品色彩饱和度提高,能超出传统印刷的20%。
②网点还原好。印版是平凹版,压印转移时向四周扩散程度较小,网点增大率降低50%,且不使用润版液,网点更清晰。
③印刷密度高。由于网点增大率小,可适当提高印刷密度,印出清晰的色调、高分辨率和高亮度的精美图像和细小文字及精密图像。
④因为不用水,无须调节水墨平衡,可选择的承印物更多,如在传统胶印无法印刷的金属箔纸、塑料和薄膜上的印刷表现出色。
⑤不使用润版液,还使双面印刷机套印准确,尤其是薄纸印刷。
(2)印刷速度和生产效率高
因为无水胶印印刷时不用调节水墨平衡,印前准备时间比传统胶印缩短40%,过版纸消耗降低30%~40%,且不使用印刷润版液。不仅节省印刷准备时间和成本,还能实现高品质、高效率生产。
(3)利于环境保护
无水胶印过程中不使用传统胶印润版液等含有挥发性溶剂的化学药剂,不向空气中排放挥发性有机物,减少了环境污染,而且节约了水资源。
当然,无水胶印也有其缺点,如油墨黏度大,对纸张质量要求高;且为保证油墨黏度不受温度影响,需要配置控温系统,增加一定成本。
目前普遍使用传统光敏无水胶印版材,不同公司、不同时期研制的印版结构不尽相同,但大体结构一般分为5层(由内而外):版基、底涂层(胶合层)、亲墨的感光层(光敏层)、斥墨的硅橡胶层及保护层。
3.4.4.2 无水胶印版结构组成
(1)版基
版基是印版的支持体,要具有一定的强度和柔性,主要使用铝薄板,此外也用涂层纸、铝合金板、橡胶板和塑料板或几种材料的组合。
(2)底涂层
底涂层是把版基与感光层黏合在一起的胶层,除具有黏合作用,也起着隔热和缓冲印刷压力等作用。
(3)感光层
感光层又称光热转化层,具有亲墨性,是印刷图文的载体,是无水胶印版材的核心组成,感光层分阴图型和阳图型两种。
(4)硅橡胶层
硅橡胶与油墨的表面张力大于油墨的内聚力,所以硅橡胶层可作为印版的斥墨层。硅橡胶由二烷基聚硅氧烷与交联剂反应生成。
(5)保护层
在硅橡胶层上有时还加涂一层透光性好的聚酯或聚丙烯薄膜保护层,既可防止版面划伤又可提高曝光时的真空度。
3.4.4.3 无水胶印版制作原理
无水胶印版的制备分为阳图型(用阳图片曝光)和阴图型(用阴图片曝光),取决于版材感光层的组成。阴图片曝光后,经显影曝光部分硅橡胶脱落,露出亲墨层(图文),未曝光部分(空白)硅橡胶保留;阳图片曝光相反,显影后曝光部分感光层与硅橡胶层交联成为斥墨层,未曝光部分的硅橡胶层除去,形成亲墨层。图3-12以阴图片曝光为例说明无水胶印版制版过程。

图3-12 无水胶印阴图片制版过程示意图
无水胶印主要适合高质量、印量少、交货期短的业务,诸如增值包装、塑料卡片、不干胶标签、3D、凸镜形状应用、CD/DVD、木制品塑封等,特别值得应用于一些极限印刷领域。
因为无水胶印版材的空白部分没有水层的保护,依靠的是硅橡胶层低表面张力对油墨的排斥,所以要求无水胶印油墨有很高的内聚力,即要求有较高的黏度,以确保不脏版(空白部分不带墨)。
无水胶印不需要润版液,只有一次上墨过程。因此,要求在上墨的过程中图文部分能很好地吸附油墨,空白部分能排斥油墨。
根据油墨的表面能的参数,只要图文部分的表面能高于油墨,空白部分的表面能低于油墨即可。在材料的选择上,为了防止油墨对空白部分的粘脏,通常空白部分的表面能要远低于油墨的表面能。现在比较成熟的无水平版,其空白部分由硅橡胶构成,其表面能很低。图文部分选择的是具有良好的亲油传墨性能的聚酯。
无水胶印在印刷过程中,由于着墨辊等软质胶辊(橡胶材料) 的滞后圈的存在,内耗产生的热量将使油墨温度升高而导致其表面能的下降。当表面能降低到一定程度,就有可能破坏空白部分和油墨之间的正常的表面能关系,从而使空白部分起脏。因此,在印刷机的构造上必须做改进。可以在软质胶辊之间插入中空的金属串墨辊,往金属串墨辊中通空气或水等制冷介质,以控制油墨的温度。
无水胶印使用的是专用油墨,它的基本成分与传统胶印的油墨相似,在色料的选择上是没有什么区别的,主要的区别是油墨中所用的树脂即连接料部分。无水胶印油墨和传统的胶印油墨相比有以下特殊的性质。
①它需要有比传统的胶印油墨更高的黏度和黏性,才有可能提供比较大的油墨内聚力,足以大于油墨和硅胶层之间的作用力,使硅胶层表现为疏油性,这样油墨与非图文部分的硅橡胶层相斥,从而实现无水印刷。
②必须适应无水胶印特殊的流变性能。因为无水胶印油墨具有高黏度,所以它在墨辊和印版之间的流通比较困难,这就要求油墨要有特别的设计,使其有较好的流变性能。
③由于在无水胶印中温度的特殊影响,所以最好还要有一个比较宽的温度适应范围。
3.4.5 UV胶印油墨和UV无水胶印油墨参考配方
(1)UV胶印油墨参考配方
PEA 25.0
EA 25.0
脂肪酸改性EA 5.0
PUA 10.0
颜料 17.0
CaCO3 5.0
SiO2 0.5
BP 3.0
ITX 2.0
ODAB 5.0
蜡 1.0
助剂 1.5
(2)UV红色胶印油墨参考配方
PEA(PRO30037) 27
PEA(CN2282) 20
Di-TMPTA 11
(EO)3TMPTA 2
907 3
TZT 2
KBI 5
活性胺 (CN373) 2
红颜料 (PR 57∶1) 20
滑石粉 6
聚乙烯蜡 2
(3)UV黄色胶印油墨参考配方
PEA(PRO20071) 20
PEA(CN790) 30
Di-TMPTA 10
(EO)3TMPTA 5
907 2
TZT 2
KBI 5
活性胺 (CN373) 2
黄颜料 (PR 57∶1) 14
滑石粉 8
聚乙烯蜡 2
(4)UV蓝色胶印油墨参考配方
EA 37.3
六官能度芳香族PUA 10.4
TMPTA 31.9
酞菁蓝 18.0
丙烯酸硅氧烷酯 0.9
润湿分散剂 1.5
LFC1001 3.0
EDAB 2.0
ITX 1.0
(5)UV黑色胶印油墨参考配方
EA 21
多官能度PUA 10
多官能度PEA 10
DPHA 8
DDA 15
BP 3
ITX 3
369 3
184 1
EDAB 6
炭黑 18
颜料紫3 1
聚乙烯蜡 1
注:用于纸或卡纸。
(6)UV黑色胶印油墨参考配方
PEA(EB657) 37.3
六官能团PUA(EB220) 11.6
环氧大豆油丙烯酸酯(EB860) 6.3
甘油衍生物三丙烯酸酯(OTA480) 10.0
炭黑 12.0
酞菁蓝 1.0
滑石粉 8.0
蜡 0.5
SiO2 1.5
分散剂 3.3
369 2.5
ITX 3.0
EDAB 3.0
(7)UV白色胶印油墨参考配方
EA 25
多官能度PEA 20
DDA 10
184 4
TPO 2
TiO2 28
聚乙烯蜡 1
滑石粉 8
SiO2 2
(8)UV胶印油墨参考配方

(9)UV-LED红色胶印油墨参考配方
巯基改性PEA(LED01) 20
PUA(EB8602) 23.5
PEA(EB830) 20
胺改性聚醚丙烯酸酯(P094F) 1
酸改性甲基丙烯酸酯(EB168) 2
379 2
TPO 4
聚乙烯蜡(PEW1555) 1.5
对苯醌(UV22) 1
颜料(永固红) 25
油墨性能
细度 <5μm
黏度 23.5Pa·s
光固化速度(395nm UV-LED灯,12W/cm2) 200m/min
(10)UV-LED蓝色胶印油墨参考配方
巯基改性PEA(LED01) 23
PUA(EB284) 21
PEA(EB546) 20
胺改性聚醚丙烯酸酯(P094F) 1
酸改性甲基丙烯酸酯(EB168) 2
TMPTA 1
1173 2
819 5
聚丙烯蜡(LANCO1588) 2
对苯醌(UV22) 1
颜料(酞菁蓝) 22
油墨性能
细度 <5μm
黏度 24Pa·s
光固化速率(395nm UV-LED灯,12W/cm2) 200m/min
(11)UV无水胶印油墨参考配方

油墨性能

(12)UV无水胶印油墨参考配方
PEA 35
PUA 15
GPTA 11
TPGDA 10
369 3
ITX 2
活性胺 3
颜料 17
滑石粉 2
聚乙烯蜡 2
(13)金属用无水胶印UV油墨参考配方
环氧双丙烯酸酯 40
聚氨酯双丙烯酸酯 18
酞菁绿 18
二芳酰胺黄 2
BP 6
ITX 4
聚乙烯蜡 6
聚四氟乙烯蜡 1
Quantacure EPD 5
此墨用于啤酒罐、饮料罐及喷雾剂罐等的无水胶印。
(14)聚丙烯用无水胶印UV油墨参考配方
聚酯双丙烯酸酯(或聚氨酯双丙烯酸酯) 66
增黏剂 2
活性单体 10
混合光引发剂 6
胺活化剂 3
颜料 18
混合蜡和表面活性剂 3
滑石粉 2
该墨常常用于层压金属箔的聚丙烯或聚乙烯等承印物的无水胶印、制作不干胶标签等。